Stålfabrikasjon
Metoder – teknikker
Metodeavdelingen i engeneeringsgruppen utarbeidet
skisser som viste steg for steg hvordan komponentene skulle tilvirkes og
settes sammen og i hvilken rekkefølge. Se skisse
”Just in time” i produksjonssammenheng betyr: riktig komponent til
riktig sted til rett tid.
Dette stilte krav til arbeidslederne at de brukte resursene riktig og at
rasjonelle arbeidsmetoder ble tatt i bruk.
Produksjonskjeden startet i brennehallen der alle
plate– og profilkomponentene ble prefabrikert og posisjonsmerket. (et
merke som iflg. tegning viser hvor i konstruksjonen komponenten skal
være).
Komponentene ble transportert til montasjehallen”til rett tid” og satt
sammen og sveist til store seksjoner. Størrelse og form var forutbestemt
av hensyn til handterbarhet og montasje. (Metodeplanlegging).
I denne produksjonsfasen ble det utvist stor
kreativitet med hensyn til å starte på riktig sted. Det ble i stor
utstrekning brukt ”gigger”for å holde komponentene på plass under
sammenstillings-/ sveiseoperasjonene. Dette var av avgjørende betydning
for å redusere krympedefekter gjennom sveiseprosessen slik at snevre
dimensjonstoleranser kunne bibeholdes. Seksjonene ble så transportert
til malehallen for overflatebehandling før montasje.
Prefabrikasjon av ”rørspools” og rørsystemer
Fabrikasjon av spools og mindre systemer foregikk i
Rørhallen. Større systemer ble sammen ute i modulene. ”Rør-spool”er en
integrert del i et komplett rørsystem og sammensatt av flere ulike
rørkomponenter. Metodeavdelingen i engeneeringsgruppen utarbeidet
skisser som viste steg for steg hvordan rørkomponentene skulle
bearbeides og settes sammen og i hvilken rekkefølge. Se skisse og bilde.
Sammenbygging til ”spools” var underlagt de samme strenge toleransekrav
som stålfabrikasjon. Form og dimensjon ble simulert ved først å lageå
”jigger”. Alle spools ble både trykk- og NDE-testet før de ble innsatt i
rørsystemene i modulen.
Sammenbygging av seksjoner til moduler
En modul er i ”offshore-terminologien” en
stålkonstruksjon sammensatt av et nedre og et øvre dekk (kan være flere
flere) dekk og mellomliggende stålprofiler sveist sammen til en stiv
enhet. Denne enheten, modulen, skulle tåle å transporteres og løftes opp
på plattformen ute på oljefeltet uten at den ble deformert . Størrelse
og vekt på modulene varierte noe. En ”standard” størrelse var 16 m bred,
32 m lang og 12 m høy. Vekten varierte fra ca. 800 til ca 1500 tonn.
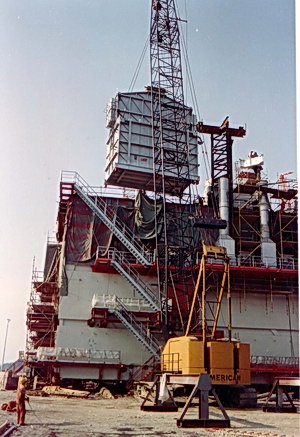
De prefabrikerte dekkseksjonene (som regel to, men
det kunne være flere) ble ute på montasjeområdet nøyaktig posisjonert på
sliskebanene. Før sammensveisingen av dekkseksjonene startet, ble
dekktoppen nivellert opp i riktig høyde med svært små toleranser.
Toleransekrav til dimensjon og retthet var også snevre. Sveisekrymp og
eventuelle deformasjoner måtte beregnes og kompenseres for.
Neste byggefase var å installere stålprofilene,
søylene og diagonalene, mellom dekkene. Avhengig av om store komponenter
skulle løftes inn, ble så toppdekket løftet på plass og sveist til de
mellomliggende profilene. Kraftige ”løfteører”ble installert som en
integrert del av konstruksjonen. Disse kunne ha en høyde på 2 meter,
bredde 70-80 cm og en tykkelse på 15 cm på det tykkeste.
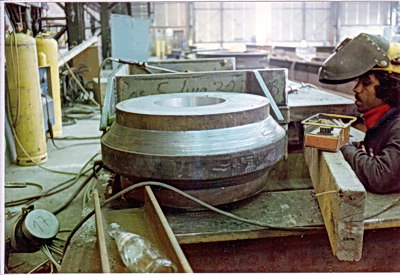
Hele byggeprosessen var gjenstand for nitid
kontroll mhp dimmensjon, retthet og utførelse av sveis. For å skjerme
mot klimatiske faktorer som hadde negativ innvirkning på spesielt
sveise- og malerarbeidet, ble hele konstruksjonen innebygd med
stillasematerialer og presenninger. Store, prefabrikerte takseksjoner
ble satt over det hele.
Å holde en akseltabel temperatur inne i disse
”husene” var en stor utfordring. Det ble anskaffet flere store
oljeslukende varmluftkanoner. Det ble etablert kontinuerlig fyringsvakt.
Når det sto flere slike ”modulhus” ute på montasjeområdet samtidig, gikk
det en tankbil med fyringsolje kontinuerlig mellom Vigor og Trondheim.
Sveisestedene ble innebygd med presenningtelt så
sveiserne så vidt kunne bevege seg i. Tilstrekkelig varme (el- og gass),
ble tilført. sveisestedene for å oppnå samme ståltemperatur som i
materialkvalifiseringen. Etter endt sveising ble sveiseforbindelsene
langsomt avkjølt. (Se
Sveisekrav)

Inventaret i modulene varierte alt etter hvilken
funksjon modulen skulle ha ute på oljeplattformen:
Olje/gass behandlings-(treatment)modul, kompressor-modul, ”power”- modul
(elektriske generatorer drevet av gassturbiner). Disse komponentene var
så store og tunge at de ble plassert (løftet/slisket) inn på plass før
modulen ble ”lukket”. Utstyrsmodulene ble alltid testet før de var klare
for utskipning ”fullskalatest”. Gassturbinene var ikke akkurat lydløse.
Det ble derfor sendt ut varsel gjennom lokalavisen.
Modulene ble alltid veid før utlasting. Dette ble gjort med veieceller
plassert mellom modul og sliskebane. Stor nøyaktighet.
Siste malingsstrøket ble lagt på, alle kontroller
og tester var godkjent og dokumentert, og modulen var klar for
utskipning.
| Neste:
Utskipning |
|